Quality Control in a Wooden Toy Factory: Ensuring Safety and Excellence
- Share
- publisher
- Forestoy
- Issue Time
- Jan 9,2025
Summary
The quality control (QC) process is essential in a wooden toy factory to ensure that every product is safe, durable, and meets industry standards.
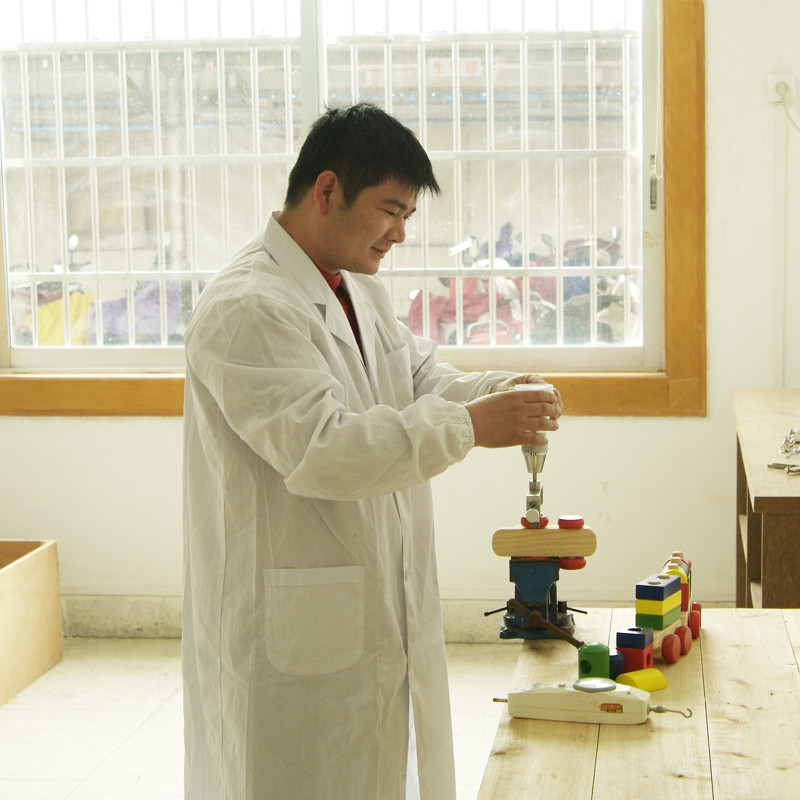
The quality control (QC) process is essential in a wooden toy factory to ensure that every product is safe, durable, and meets industry standards. This is particularly crucial in the toy manufacturing industry, where children’s safety is a top priority. A robust QC system helps to minimize risks, maintain high-quality standards, and meet both local and international regulations. Let’s dive into how QC is managed in a wooden toy factory.
1. Raw Material Inspection
The first stage of quality control in wooden toy production begins with the inspection of raw materials. Wood must be free from defects such as cracks, knots, or improper drying.
Wood Quality Check: Ensuring the wood is sourced from certified, sustainable forests (such as FSC-certified wood).
Moisture Level Testing: Wood must have the correct moisture level to avoid warping during production.
2. Design and Prototype Evaluation
Once the raw materials are approved, the design team creates a prototype of the toy. At this stage, QC professionals assess whether the design is feasible and safe for production.
Key considerations include:
Age-appropriate Design: Ensuring the design does not pose any choking hazards, sharp edges, or potential for breakage.
Stability and Durability: Ensuring the toy can withstand rough handling by children without breaking.
Non-toxic Materials: Ensuring that the paint, finishes, or other components used are child-safe and non-toxic.
3. Production Process Monitoring
During the actual manufacturing process, quality control is closely monitored at each step.
Machine Calibration and Maintenance: Ensuring all machinery is functioning properly, and there are no mechanical defects in the production line that could affect the toys' quality.
In-process Inspections: QC personnel perform random inspections on toys being manufactured to check for defects or non-compliance.
Component Inspection: Checking individual parts like wheels, legs, or handles for uniformity and structural integrity.
4. Visual and Functional Inspection
After the toys are assembled, they undergo visual and functional inspections to ensure that each piece is properly constructed. Inspection points are:
Surface Finish: The paint, stain, or other finishes must be free from cracks, peeling, or fading.
Assembly Check: Ensuring that all parts are securely fastened and there are no loose pieces or sharp edges.
Moving Parts Check: If the toy has moving parts (such as wheels or doors), they must be functional and free of obstruction.
5. Safety Testing and Compliance
In addition to visual inspection, wooden toys undergo rigorous safety testing to meet international standards such as EN71 (European toy safety standard) and ASTM F963 (American toy safety standard). These tests are designed to ensure that the toys are safe for children and that they won’t pose any choking, suffocation, or other hazards.
The testing process includes:
Mechanical and Physical Testing: Ensuring the toy can withstand the rough handling it might receive during play. This includes testing for strength, durability, and resistance to breakage.
Chemical Testing: Verifying that the paint, varnish, and materials used do not contain harmful substances like lead, cadmium, or other toxic chemicals.
Age-appropriate Testing: Toys are tested to ensure they are suitable for the target age group. For example, smaller parts that could pose a choking hazard are tested for children under 3 years old.
6. Packaging Inspection
Proper packaging is crucial to prevent damage during shipping, while also ensuring that the toy is presented attractively for sale. The important points are:
Packaging Material: Ensuring that packaging is durable and protective while also being eco-friendly.
Labeling Compliance: Verifying that all labels meet regulatory standards (such as CE, ASTM, and other required certifications).
Clear Instructions: Ensuring that assembly instructions (if necessary) and safety warnings are clearly displayed in the packaging.
7. Final Product Inspection and Batch Testing
Before the toys are shipped out, a final inspection is conducted. This inspection involves:
Random Sampling: A certain percentage of toys from each batch are randomly selected for further inspection. This helps identify any defects or non-compliance issues that may not have been caught earlier.
Functionality Testing: Testing the functionality of toys, such as checking if moving parts work smoothly and that no parts are loose or sharp.
Safety Compliance: Ensuring the toys pass all required safety tests and certifications before being dispatched.
8. Shipping and Post-production Follow-up
Once the toys pass QC and are ready for shipment, the factory ensures that they are stored and shipped in the best possible conditions to prevent damage. Additionally, after the toys reach customers, the factory may conduct a follow-up to collect feedback and improve future products.
Implementing a strict quality control process in a wooden toy factory is essential for ensuring product safety, durability, and customer satisfaction. From sourcing materials to post-production shipping, QC plays a vital role at every stage of production. By prioritizing rigorous inspections, testing, and continuous improvement, a wooden toy manufacturer can ensure that its products are both safe and high-quality, meeting the expectations of consumers and regulatory bodies alike.
Equipped with advanced facilities, we maintain efficient production, strict quality control, and on-time delivery. Dedicated to enriching children's play, we are your trusted partner for high-quality wooden toys. Contact us for custom solutions and a free brochure!